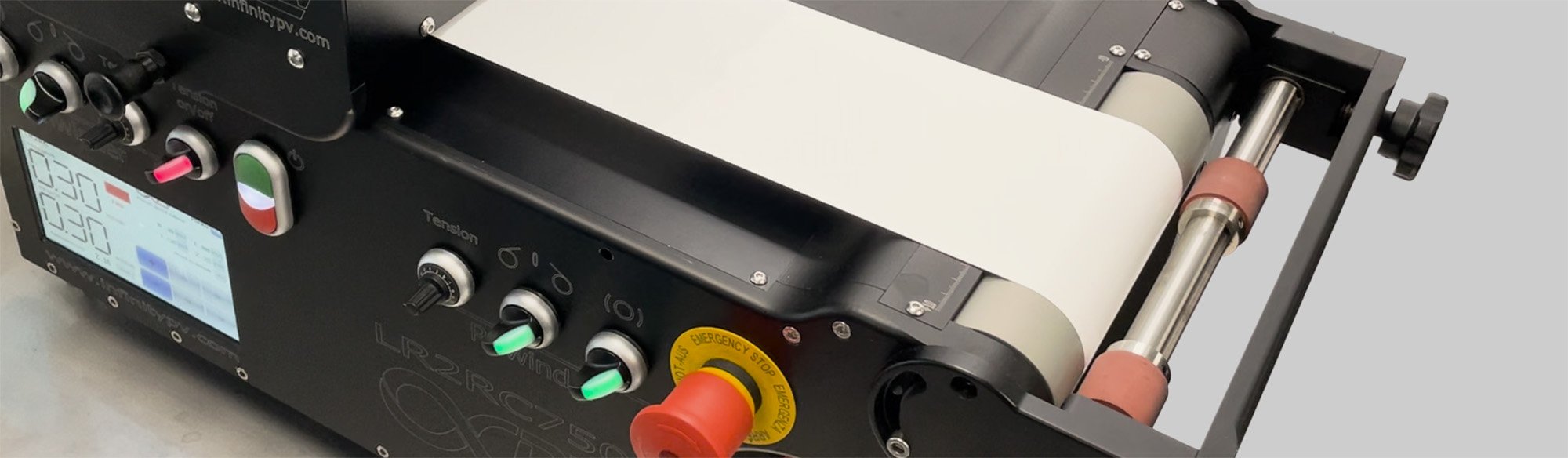
Slot-Die Coating for Sensors: Precision Coating for Printed and Flexible Devices
Slot-Die Coating for Printed and Flexible Sensors
The demand for printed and flexible sensors is rapidly growing across industries such as healthcare, environmental monitoring, industrial IoT, and consumer electronics. These sensors often rely on multilayer structures consisting of conductive, dielectric, and sensing materials, which must be applied with precision and consistency. Slot-die coating is becoming a go-to technique for researchers and developers working in this space due to its ability to deliver high-quality thin films on flexible or rigid substrates.
Slot-die coating enables the controlled deposition of functional inks for pressure sensors, temperature sensors, biosensors, chemical detectors, and more. Each sensing layer can be applied with uniform thickness and repeatable accuracy — a critical factor in ensuring consistent sensor performance across large areas. Whether you're working with carbon-based materials, polymer composites, metal oxides, or nanomaterials, slot-die coating offers a versatile and scalable solution for testing and optimizing your sensor designs.
Enabling Scalable Fabrication of High-Performance Sensors
One of the biggest challenges in bringing printed sensors to market is maintaining consistent sensitivity and response across production batches. Slot-die coating solves this by offering excellent control over process parameters like coating speed, fluid flow, substrate temperature, and drying conditions. This helps minimize defects, improve device yield, and reduce variability in sensor behavior.
In a lab setting, researchers can use slot-die coating to iterate rapidly on new material combinations or optimize the active sensing layer for selectivity, response time, or stability. As development moves toward pilot or full-scale production, the same technique can be scaled using roll-to-roll platforms with minimal adjustment. This makes slot-die coating ideal not only for prototyping but also for manufacturing next-generation wearable sensors, environmental tags, or industrial sensor arrays.
Advantages of Slot-Die Coating for Sensors
Uniformity and Sensitivity Control: Sensor accuracy often depends on the evenness and repeatability of the sensing layer. Slot-die coating provides smooth, uniform coatings with controlled thickness — essential for tuning the electrical or chemical response of the device.
Scalable from Lab to Manufacturing: Slot-die coating supports a seamless transition from small-scale experiments to large-area and high-throughput production. This scalability is particularly important for disposable sensors or large sensor networks where cost and consistency are critical.
Compatible with a Range of Functional Inks: From conductive polymers to enzymatic coatings and nanomaterial-based sensing elements, slot-die coating handles diverse material systems. It supports both aqueous and solvent-based formulations, making it suitable for a wide spectrum of applications.
Low Material Waste and High Efficiency: As a pre-metered process, slot-die coating reduces ink waste compared to spray or screen printing. This efficiency not only lowers cost but also supports sustainable manufacturing practices — increasingly important in sensor applications tied to environmental monitoring.
Ideal for Multilayer Sensor Designs: Complex sensor architectures often involve multiple stacked layers, including encapsulation, reference electrodes, or insulation barriers. Slot-die coating simplifies this by allowing accurate deposition of each layer without compromising the underlying structure.
Coating Equipment for Printed Transistors
Selecting the appropriate processing method for your packaging applications depends on production scale, material needs, and specific requirements.
Slot-die Coater
We recommend choosing sheet-based processing, such as the Slot-die Coater, for lab-scale research, prototyping, and small-batch production. This method offers the flexibility to test formulations, adjust parameters, and produce precise coatings in limited quantities—ideal for early-stage development and specialized applications.
Laboratory Roll-to-Roll Coater
Choose Roll-to-Roll (R2R) Processing, such as the Laboratory Roll-to-Roll Coater, when you need to scale up lab-scale results for continuous, high-throughput production. While still on a laboratory scale, R2R processing ensures uniformity and consistency over long substrates, making it suitable for applications that will eventually transition to larger-scale manufacturing.
Your Trusted Partner in Printed Transistors
With decades of experience in printed electronics, our expert team is here to provide in-depth guidance on choosing the right system for your needs. Whether you're exploring advanced production methods or need help fine-tuning your setup, we offer expert advice tailored to your project. Contact us to discuss how we can support your solar cell development.