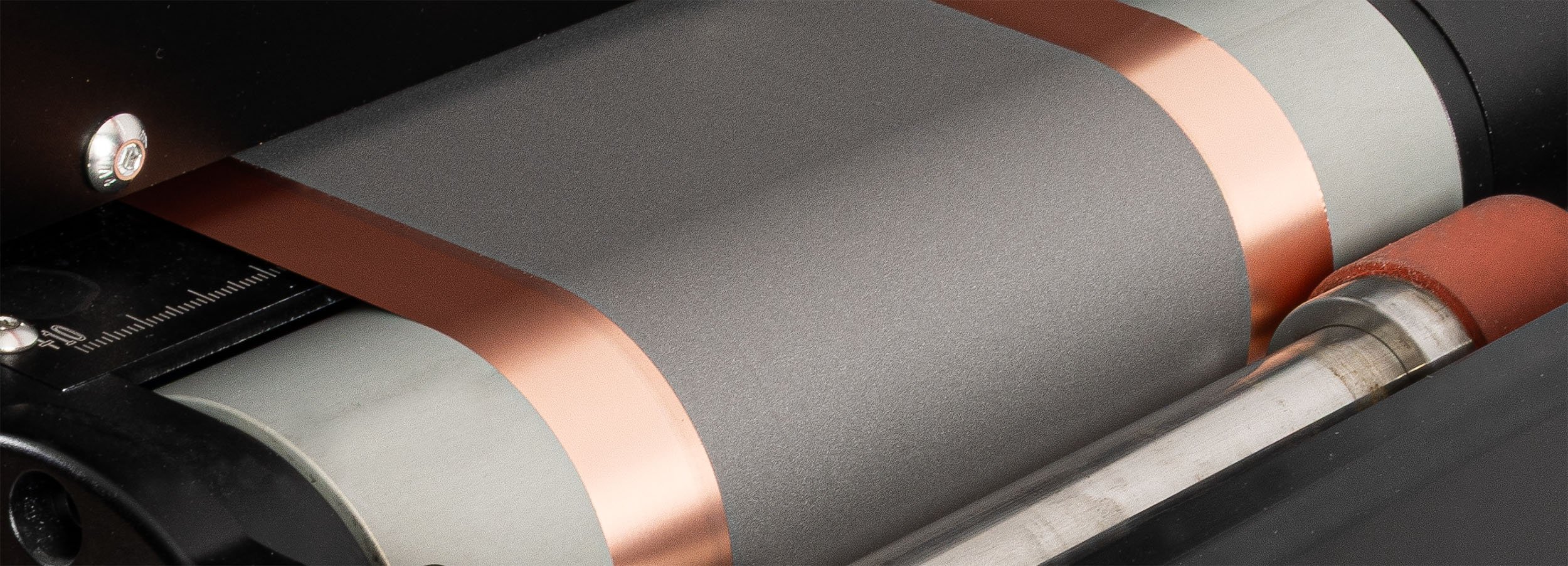
Slot-Die Coating for Scalable Battery Electrode Production
How Slot-Die Technology Can Accelerate Battery R&D
Slot-die coating is a cutting-edge solution for precise thin-film deposition in the battery industry, crucial for optimizing material layers’ thickness and uniformity. This technique provides scalable control from lab to pilot scale, revolutionizing the speed and consistency of battery development. By adopting slot-die technology early in the R&D process, you can reduce risks and shorten time-to-market.
Slot-die coating advances battery R&D by offering highly precise, uniform coatings that optimize performance, reduce material waste, and lower production costs. It enables scalability from lab to production, ensuring quality consistency and accelerating development timelines. In industrial battery manufacturing, slot-die coating is a widely used technique, and its adoption early in the R&D phase helps streamline the transition to full-scale production.
Cost-Effective Path to Scaling Your Battery Research
At infinityPV, we offer modular coating platforms and specialized components designed to advance next-generation thin-film battery technologies. Our solutions ensure precise thin-film deposition, uniform coatings, reliable surface treatments, and controlled drying—essential for optimizing the performance, stability, and scalability of thin-film batteries, including solid-state, lithium-based, and emerging flexible energy storage solutions.
Choosing the Right Coating Method: Slot-Die vs Knife Coating
Slot-Die Coating
Slot-die coating is particularly useful for lab-scale processing of printed batteries due to its ability to produce highly uniform and reproducible coatings on substrates, ensuring consistent electrochemical performance in experimental setups. The method allows for precise control over layer thickness, enabling researchers to fine-tune material properties and optimize battery designs. Additionally, slot-die coating facilitates the use of various formulations and substrates, making it an adaptable choice for prototyping and material testing.
Knife Coating
Knife coating is an alternative to slot-die coating and offers an effective method for quickly testing different battery slurry formulations. It allows researchers to easily apply various slurries onto substrates in a controlled manner, enabling the rapid evaluation of how different compositions affect battery performance. Knife coating is simpler, making it ideal for iterative experimentation. The ability to produce varying layer thicknesses provides insights into slurry properties and their impact on electrochemical outcomes.
Coating Equipment for Thin-film Battery Applications
We enable you to quickly coat exceptional electrodes with our advanced coating method, ideal for energy storage device R&D. Our slot-die coating systems are recognized as the industry standard in global battery research, offering precise control over slurry dosage, wet film thickness, and coating speed.
The SDC Battery Coater Pro is specifically designed for researchers dedicated to developing and optimizing battery materials. It facilitates a seamless transition from research to commercialization.
Customized for lab-scale research and development, this system facilitates the efficient application of battery electrode coatings.
With a substrate processing width of up to 305 mm, you are well-equipped to initiate pilot-scale production of your battery technology.
Video: How to Make a Thin-film Battery
The Slurry Coater is a fundamental wet film forming tool for the Laboratory Roll-to-Roll Coater platform enabling lab scale production of advanced functional thin films.
Your Trusted Partner in Battery Innovation
With decades of experience in printed electronics, our expert team is here to provide in-depth guidance on choosing the right system for your needs. Whether you're exploring advanced production methods or need help fine-tuning your setup, we offer expert advice tailored to your project. Contact us to discuss how we can support your solar cell development.
Sheet or Roll-to-Roll Processing of Battery Slurries?
When selecting between sheet and roll-to-roll (R2R) processing for battery slurries at the lab scale, consider the following factors:
Material Requirements: If you are working with smaller batches or highly specialized materials, sheet processing may be more suitable. R2R is typically better for continuous production but may require more standardization in materials.
Coating Quality: For applications needing high precision and uniformity, sheet processing offers better control over coating thickness and can accommodate various substrates more easily. R2R might require optimization to achieve similar results.
Process Time and Efficiency: R2R is generally faster and more efficient for scaling up, but it may require more setup time initially. If rapid testing and iteration are essential, sheet processing might be more beneficial for quick evaluations.
Substrate Size and Type: Consider the size and flexibility of substrates. R2R is excellent for flexible materials and large-scale production, while sheet processing might be preferable for fixed-size or rigid substrates.
Cost Considerations: R2R systems can be more costly upfront due to their complexity and automation requirements. For small-scale experiments, sheet coating might be more cost-effective, allowing for flexibility without significant investment.
Experimentation Needs: If your research involves frequent changes to formulations or coatings, sheet processing allows for easier adjustments and rapid prototyping compared to R2R.
In summary, if your primary focus is on precision and rapid testing of varying formulations, sheet processing may be the better choice. In contrast, if you aim to scale up production efficiently or work with flexible materials, roll-to-roll processing could be more advantageous.
Why Choose the Right Supplier?
Choosing the right supplier is key to ensuring smooth transitions across different stages of development. With a consistent supplier, you can rely on the same slot-die heads, software, operating protocols, and calibration standards, making scaling easier and more efficient.
How You Can Stay Ahead of the Curve
Mimic Full-Scale Production: Slot-die technology enables you to replicate full-scale production processes at a smaller scale, saving time when transitioning to larger-scale machines and industrial production.
Production-Level Quality on a Smaller Scale: Slot-die coating at the lab scale provides consistent, high-quality output with a smaller footprint, allowing you to identify and resolve issues early before scaling up.
Leverage Early Experiences: Using smaller machines helps build expertise and troubleshooting skills, ensuring a smoother scale-up process when moving to pilot production.
Get Started Today
Ready to scale your battery R&D with cutting-edge coating technology? Contact us today to learn more about how our slot-die coating systems can streamline your research process, from lab-scale testing to full-scale production.