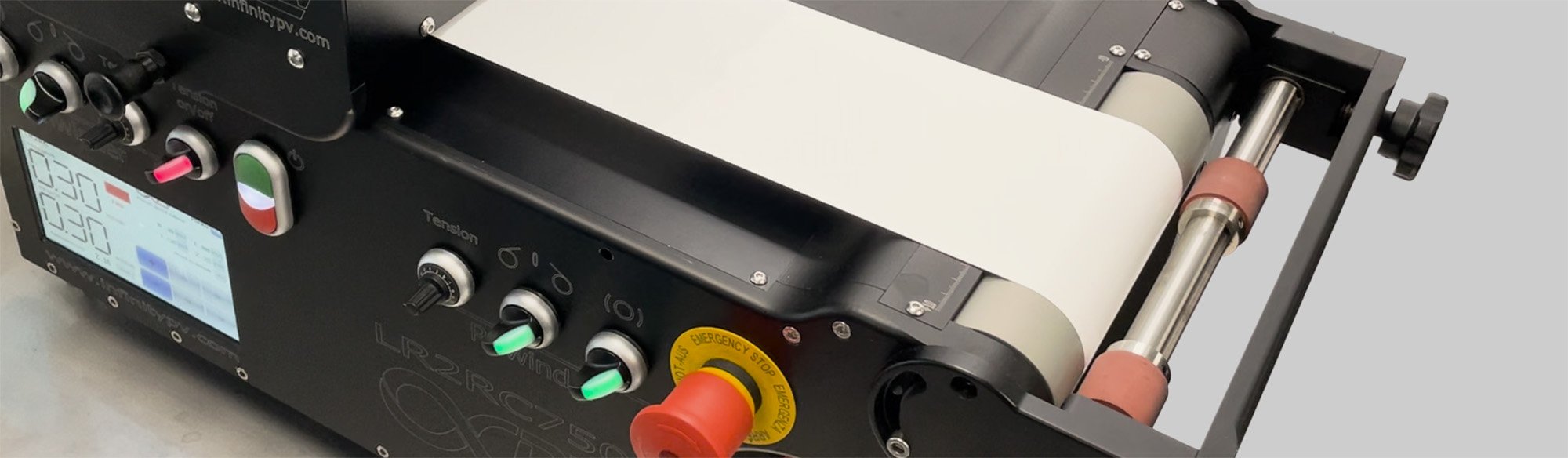
How Slot-Die Coating Revolutionizes Packaging Materials
The Role of Slot-Die Coating in Material Development
In the fast‑paced packaging industry, staying ahead of market trends and meeting consumer demands for efficiency, cost‑effectiveness, and sustainability is crucial. As brands and researchers push the boundaries of what packaging can do—extending shelf life, adding functionality, reducing waste—the development of new materials becomes the linchpin of innovation. Slot‑die coating technology sits at the forefront of this transformation, offering manufacturers precise, repeatable control over the application of thin films and coatings that define modern packaging performance.
Slot‑die coating works by pumping a liquid formulation through a narrow, precision‑machined die onto a continuously moving substrate. By fine‑tuning parameters such as the die gap, coating speed, material viscosity, and drying profile, engineers can deposit ultra‑uniform layers—whether it’s a moisture barrier, an adhesive primer, or a specialized functional coating—down to the micron level. This level of control not only ensures consistent product quality across large production runs, but also accelerates R&D cycles, enabling rapid testing and optimization of new formulations for packaging applications.
Lamination in Packaging Development
Lamination is another essential technique used in packaging, particularly for flexible materials. It involves bonding multiple layers of materials together to enhance strength, durability, and functionality. When combined with slot-die coating, lamination becomes an even more powerful tool for creating multi-functional packaging. This combination allows manufacturers to integrate different properties, such as barrier protection, heat resistance, and visual appeal, into a single packaging solution. By applying functional coatings via slot-die coating, followed by lamination, packaging designers can create materials that offer a wide array of benefits, making them more adaptable and sustainable.
Testing and Optimizing New Materials
Slot-die coating enables manufacturers to experiment with a range of materials and coatings, helping to optimize packaging performance. Key applications include:
Barrier Coatings: One of the most critical components in packaging, barrier coatings protect the contents from external factors like moisture, oxygen, and light. With slot-die coating, precise layers can be applied to optimize barrier performance and extend shelf life. Researchers can test different formulations and adjust thicknesses to enhance the performance of the final material.
Adhesive Testing: Packaging often involves bonding materials together, and slot-die coating allows for the precise application of adhesives. This enables researchers to experiment with adhesive properties such as peel strength, bonding performance, and reaction under different environmental conditions. The controlled application ensures accurate results during testing, essential for developing reliable packaging solutions.
Functional Coatings: Beyond basic protection, packaging materials can benefit from functional coatings that provide heat resistance, anti-fogging properties, UV protection, or even antibacterial effects. Slot-die coating is perfect for applying these additional layers, offering an effective way to enhance packaging performance and meet specific consumer needs.
Coating Equipment for Packaging Applications
Selecting the appropriate processing method for your packaging applications depends on production scale, material needs, and specific requirements.
Slot-die Coater
We recommend choosing sheet-based processing, such as the Slot-die Coater, for lab-scale research, prototyping, and small-batch production. This method offers the flexibility to test formulations, adjust parameters, and produce precise coatings in limited quantities—ideal for early-stage development and specialized applications.
Laboratory Roll-to-Roll Coater
Choose Roll-to-Roll (R2R) Processing, such as the Laboratory Roll-to-Roll Coater, when you need to scale up lab-scale results for continuous, high-throughput production. While still on a laboratory scale, R2R processing ensures uniformity and consistency over long substrates, making it suitable for applications that will eventually transition to larger-scale manufacturing.
Your Trusted Partner in Packaging Solutions
With decades of experience in printed electronics, our expert team is here to provide in-depth guidance on choosing the right system for your needs. Whether you're exploring advanced production methods or need help fine-tuning your setup, we offer expert advice tailored to your project. Contact us to discuss how we can support your solar cell development.