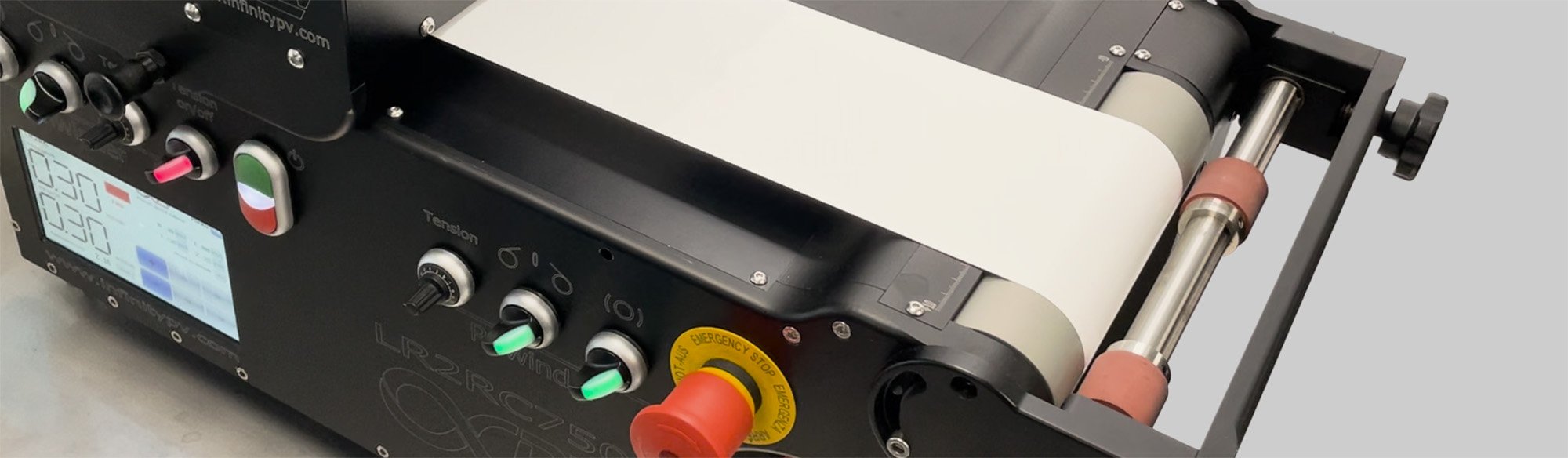
Slot-Die Coating Technology for Adhesive Films
Slot-Die Coating for Adhesives
Slot-die coating has become an essential technique in the application of adhesives, offering a highly accurate and scalable method for depositing thin films of liquid material onto a substrate. In industrial manufacturing, especially in sectors like electronics, automotive, packaging, energy, and healthcare, adhesives often play a critical role in product performance. The precision, efficiency, and control offered by slot-die coating make it an increasingly preferred choice for companies seeking to optimize adhesive bonding in high-value, high-volume, or high-performance applications.
Benefits of Slot-Die Coating for Adhesives
Precision and Uniformity: Slot-die coating offers exceptional control over adhesive thickness, ensuring consistent layer deposition across the substrate. This precision reduces waste, ensures product performance, and meets tight manufacturing tolerances, especially critical in electronics, medical devices, and optics.
Clean and Contactless Application: The non-contact nature of slot-die coating minimizes contamination and mechanical damage. This makes it ideal for sensitive substrates and cleanroom environments where maintaining product integrity is essential.
Material and Cost Efficiency: As a pre-metered process, slot-die coating uses only the adhesive needed, eliminating overspray and excess application. This not only lowers material costs but also reduces environmental impact and post-process cleanup.
Scalable and Repeatable: Slot-die coating is inherently scalable, from laboratory setups to full-scale roll-to-roll production, while maintaining process consistency. Once optimized, coating parameters can be reliably replicated across batches and production lines.
Versatile and Customizable: The method supports a wide range of adhesive types and can be tailored through die design, web handling, and add-ons like edge guides, heating, or surface treatment. This flexibility allows it to serve diverse industries, from flexible electronics to packaging.
Why Use Slot-Die Coating for Adhesive Applications?
Adhesives are often used in high-performance, multilayer systems where the bonding layer must be uniform, durable, and clean. Whether you're laminating films, attaching electronic components, or producing pressure-sensitive labels, the characteristics of the adhesive coating directly impact product reliability and performance. Slot-die coating provides several specific advantages for these applications.
First, it offers exceptional control over coating thickness and uniformity. This allows manufacturers to use the minimum amount of adhesive necessary for effective bonding, which reduces material waste and improves cost efficiency. In industries where expensive functional adhesives are used—such as optically clear adhesives in displays or conductive adhesives in flexible electronics—this level of precision is not just beneficial; it is often essential.
Second, slot-die coating is a clean, contactless method. This means it avoids the contamination risks and mechanical disturbances associated with techniques like roll coating or screen printing. For medical and electronic applications, where particle contamination or mechanical stress can lead to product failure, slot-die coating ensures a cleaner, more reliable process.
Third, the scalability of slot-die systems makes them ideal for both research and production environments. The same principles that apply in a laboratory coater can be scaled up to wide-web, high-throughput manufacturing lines. This simplifies the transition from prototype to product and allows process parameters developed during R&D to be transferred directly to industrial production.
Finally, slot-die coating is compatible with a wide range of adhesive types, including solvent-based, water-based, UV-curable, pressure-sensitive, and hot melt formulations. As long as the rheological properties of the adhesive fall within a manageable viscosity range, slot-die technology can be adapted to handle it—often with the addition of temperature control or customized shim sets.
Coating Equipment for Adhesive Applications
Selecting the appropriate processing method for your adhesive applications depends on production scale, material needs, and specific requirements.
Slot-die Coater
We recommend choosing sheet-based processing, such as the Slot-die Coater, for lab-scale research, prototyping, and small-batch production. This method offers the flexibility to test formulations, adjust parameters, and produce precise coatings in limited quantities—ideal for early-stage development and specialized applications.
Laboratory Roll-to-Roll Coater
Choose Roll-to-Roll (R2R) Processing, such as the Laboratory Roll-to-Roll Coater, when you need to scale up lab-scale results for continuous, high-throughput production. While still on a laboratory scale, R2R processing ensures uniformity and consistency over long substrates, making it suitable for applications that will eventually transition to larger-scale manufacturing.
Your Trusted Partner in Adhesive Coating Solutions
With decades of experience in printed electronics, our expert team is here to provide in-depth guidance on choosing the right system for your needs. Whether you're exploring advanced production methods or need help fine-tuning your setup, we offer expert advice tailored to your project. Contact us to discuss how we can support your solar cell development.
Adhesive Types and Substrate Considerations
The versatility of slot-die coating means it can be used for a broad array of adhesive formulations. Pressure-sensitive adhesives (PSAs) are among the most commonly coated, particularly for applications in labels, medical tapes, and consumer goods. These adhesives require precise control to avoid uneven tackiness, wrinkling, or excess residue. Slot-die coating enables smooth and repeatable PSA application, often directly onto silicone-coated release liners or transparent films.
Optically clear adhesives (OCAs) represent another major use case, particularly in the electronics and display industries. OCAs are used to laminate layers in devices like smartphones, tablets, and automotive displays. These adhesives must be free of bubbles, haze, and thickness variation. Slot-die coating is uniquely suited to achieve this level of uniformity, especially when paired with in-line lamination or vacuum processing.
Other common adhesive types include UV-curable adhesives for optical and structural bonding, and heat-activated adhesives used in textile laminates and automotive assemblies. In battery and fuel cell manufacturing, functional adhesives may be used to bond or encapsulate sensitive materials such as electrodes, separators, or barrier films. These require precise coating patterns, edge control, and compatibility with low-tension substrates—all of which slot-die systems can accommodate.
The choice of substrate is equally critical. Slot-die coating works with a wide range of flexible and rigid substrates including PET, PEN, PI (polyimide), paper, glass, and metal foils. Surface treatment methods such as corona or plasma treatment are often used to increase surface energy and improve adhesive wetting, especially when working with low-energy materials like polyethylene or polypropylene. Good surface preparation ensures that the adhesive bonds as intended and reduces the likelihood of defects during downstream processing.
Process Challenges and Innovations
Like any coating technique, slot-die coating comes with challenges. Setup can be time-consuming, particularly when dialing in flow rates, shim thickness, gap height, and substrate speed. Adhesives with high viscosity or shear sensitivity may require special handling, such as heating or shear-controlled pump systems. Edge control is also a common concern—without proper guides or containment strategies, adhesive can bleed beyond the target coating area.
Drying and curing processes must also be carefully matched to the adhesive and substrate. For example, UV-curable adhesives require uniform UV exposure and inert gas environments to fully cure without degradation. Thermal adhesives may require controlled ramp-up and cool-down profiles to avoid deformation or premature bonding.
Recent innovations are addressing many of these challenges. Modular coating systems now allow rapid changeover between adhesive types and coating formats. In-line sensors and closed-loop feedback systems are improving process control and repeatability. And digital slot-die heads capable of patterned or intermittent coating are expanding the range of adhesive applications that can be served.
Industrial Applications and Integration in Manufacturing Lines
In industrial settings, slot-die coating is integrated into roll-to-roll production lines where it is often combined with other processes such as drying, curing, lamination, or inspection. A typical adhesive coating line may include the slot-die head, a pump system, web tension control, a pre-treatment station, and one or more curing modules (such as hot air ovens or UV curing units). This modular approach makes it easy to tailor the coating system to the specific requirements of the adhesive and substrate.
In the electronics industry, slot-die coating is commonly used to apply bonding layers for display modules, touchscreens, printed circuit boards, and wearable sensors. These applications demand tight control over thickness and edge definition, especially where patterned adhesive coatings are required. In automotive manufacturing, adhesive films are used for mounting sensors, laminating protective films, and assembling battery packs, all of which benefit from slot-die’s precision and consistency.
In medical device manufacturing, slot-die is used to coat breathable PSAs onto film substrates for bandages and biosensor patches. Here, the technology provides a reliable method for coating adhesives that come into direct contact with human skin, where comfort and performance are critical.
Flexible packaging is another growth area. As manufacturers seek more sustainable and recyclable materials, water-based adhesives applied via slot-die systems offer an environmentally friendly alternative to solvent-based lamination. In food and pharmaceutical packaging, the clean application and minimal waste characteristics of slot-die coating provide clear process advantages.
Ready to Optimize Your Adhesive Coating Process?
Slot-die coating is a robust, scalable, and highly accurate method for applying adhesives across a wide range of industries. Its ability to precisely control coating thickness, minimize waste, and ensure clean, defect-free application makes it especially valuable for high-performance products in electronics, medical devices, energy systems, and beyond.
For professionals working in adhesive formulation, product development, or process engineering, understanding how slot-die coating integrates into adhesive systems is key to building more efficient, sustainable, and reliable manufacturing lines. As adhesive technologies advance, slot-die coating remains one of the most powerful tools for transforming liquid bonding agents into consistent, high-performance functional layers.
Contact us to learn how slot-die coating can enhance your adhesive application process and how our systems can be tailored to your specific needs.