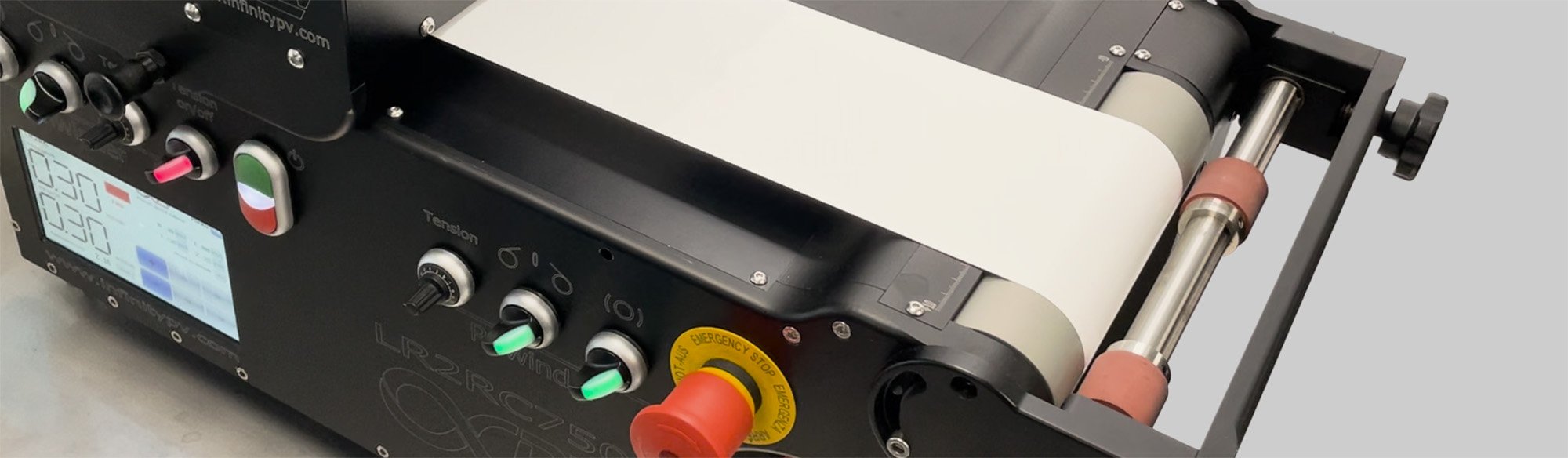
Slot-Die Coating for Pharmaceuticals and Medicine
Why Use Slot-die Coating for Pharma & Medicine
Slot-die coating is an advanced and highly controlled deposition technique that is particularly well-suited for pharmaceutical and medical applications. Its ability to produce uniform, precise, and reproducible thin films makes it an essential tool for research and development in drug delivery, diagnostic devices, and medical coatings. Unlike traditional coating methods, slot-die coating enables the controlled deposition of functional materials onto various substrates, ensuring batch-to-batch consistency and scalability from laboratory-scale development to full-scale production.
Advantages of Slot-Die Coating in Pharma & Medicine
Precision and Uniformity: Ensures consistent coating thickness and material distribution, which is critical for pharmaceutical applications requiring dosage control.
Scalability: Enables a seamless transition from laboratory-scale R&D to industrial-scale production while maintaining quality.
Material Efficiency: Minimizes material waste by applying precise volumes of expensive pharmaceutical ingredients.
Customizability: Allows for the deposition of a wide range of materials, including bioactive compounds, polymers, and nanomaterials.
Multi-Layer Capabilities: Facilitates the controlled deposition of multiple layers, enabling the development of complex drug delivery systems and advanced medical devices.
Compatibility with Various Substrates: Can be used on flexible films, biocompatible materials, and rigid substrates, supporting diverse applications in medical technology.
Applications of Slot-die Coating in Pharma & Medicine
Antimicrobial Coatings: Slot-die coating enables the uniform deposition of antimicrobial agents on surfaces, optimizing their effectiveness in preventing bacterial and viral contamination. This is particularly valuable for medical devices, implants, and hospital surfaces where infection control is critical.
Diagnostic Strips: The fabrication of diagnostic strips benefits from slot-die coating’s precision, which allows for the controlled application of antibodies, enzymes, and reactive materials. This ensures high sensitivity and specificity in detecting biomarkers in blood, urine, and other bodily fluids.
Transdermal Drug Delivery Patches: Slot-die coating is used to coat biocompatible substrates with therapeutic agents, enabling controlled drug release. The uniform application improves the consistency and effectiveness of drug delivery patches, enhancing patient compliance and treatment efficacy.
Nanomedicine Integration: The incorporation of nanoparticles into coatings can enhance drug delivery and targeting efficiency. Slot-die coating enables the uniform dispersion of nanoparticles in thin films, improving therapeutic outcomes and drug bioavailability.
Thin Film Pharmaceuticals: Oral thin films (OTFs) and dissolvable drug-loaded films benefit from slot-die coating’s ability to precisely control thickness and composition. This method enhances drug solubility, stability, and absorption, making it ideal for fast-dissolving medications.
Wearable Biosensors & Medical Devices: Wearable health monitoring devices, such as glucose sensors and biosensors, rely on slot-die coating for the uniform application of conductive and bioactive layers. This improves sensor sensitivity, accuracy, and reliability in real-time health monitoring.
Coating Equipment for Pharmaceuticals and Medicine
Selecting the appropriate processing method for your pharmaceutical or medical applications depends on production scale, material needs, and specific requirements.
Slot-die Coater
We recommend choosing sheet-based processing, such as the Slot-die Coater, for lab-scale research, prototyping, and small-batch production. This method offers the flexibility to test formulations, adjust parameters, and produce precise coatings in limited quantities—ideal for early-stage development and specialized applications.
Laboratory Roll-to-Roll Coater
Choose Roll-to-Roll (R2R) Processing, such as the Laboratory Roll-to-Roll Coater, when you need to scale up lab-scale results for continuous, high-throughput production. While still on a laboratory scale, R2R processing ensures uniformity and consistency over long substrates, making it suitable for applications that will eventually transition to larger-scale manufacturing.
Your Trusted Partner in Pharmaceutical and Medical Coating Solutions
With decades of experience in printed electronics, our expert team is here to provide in-depth guidance on choosing the right system for your needs. Whether you're exploring advanced production methods or need help fine-tuning your setup, we offer expert advice tailored to your project. Contact us to discuss how we can support your solar cell development.
Roll-to-Roll (R2R) and Sheet-Based Processing for Pharmaceutical and Medical Applications
Slot-die coating is a powerful technique for applying uniform thin films in pharmaceutical and medical applications. Depending on production needs, it can be performed using roll-to-roll (R2R) processing or sheet-based (batch) processing. R2R processing is best suited for high-throughput, continuous production, while sheet-based processing offers greater flexibility for research and small-scale applications. The choice between these methods depends on factors such as production volume, material efficiency, and scalability.
Roll-to-Roll (R2R) Processing – High-Throughput and Scalable
R2R processing is ideal for pharmaceutical and medical applications that require large-scale, consistent production. It involves continuously feeding a flexible substrate through a slot-die coater, ensuring precise material deposition across extended lengths. This method is particularly beneficial for drug delivery systems, transdermal patches, diagnostic test strips, and antimicrobial coatings, where uniformity and efficiency are critical.
One of the primary advantages of R2R processing is its high production efficiency, as continuous operation reduces downtime and maximizes throughput. Additionally, it provides superior coating consistency, minimizing batch variability and improving product reliability. Since pharmaceutical materials can be expensive, R2R processing also helps reduce material waste, making it a cost-effective choice. Another key benefit is its ability to integrate with inline drying, curing, and quality control systems, ensuring seamless production from coating to final product.
High-throughput manufacturing for continuous, large-scale production.
Enhanced uniformity for precise and reproducible coatings.
Material efficiency to minimize waste of costly pharmaceutical compounds.
Seamless process integration with drying, curing, and quality control systems.
For laboratory-scale R2R applications, the Laboratory Roll-to-Roll Coater offers a reliable platform for developing pharmaceutical coatings with precision and scalability. It enables researchers and manufacturers to optimize coating parameters before transitioning to full-scale production.
Sheet-Based (Batch) Processing – Flexible and Precise
Sheet-based processing is preferred for research and small-batch production, where precise control over coating parameters is essential. In this method, individual sheets or substrates are coated one at a time, allowing for quick adjustments to formulations and coating thickness. This makes it particularly useful for early-stage drug development, prototype medical coatings, and biosensor applications that require frequent material changes and testing.
Compared to R2R processing, sheet-based coating offers greater flexibility, making it easier to experiment with different formulations. Researchers can precisely control coating thickness, material distribution, and layer composition, ensuring that experimental coatings meet strict pharmaceutical and medical requirements. However, sheet-based processing is less scalable, as handling individual sheets increases processing time and may lead to higher material waste. This makes it better suited for low-volume, high-value applications where precision is more important than speed.
Highly flexible for research and small-batch production.
Precise control over coating parameters for experimental coatings.
Limited scalability compared to continuous R2R processing.
Potential for higher material waste when working with expensive pharmaceutical ingredients.
For laboratory-scale sheet-based applications, the Slot-Die Coater for sheets is an excellent tool, allowing researchers to fine-tune coating processes before scaling up to R2R production.
Choosing the Right Method for Your Application
Both R2R and sheet-based processing have distinct advantages depending on the needs of the pharmaceutical or medical application. For large-scale, high-throughput production, R2R processing with the Laboratory Roll-to-Roll Coater ensures efficiency and consistency. For research, formulation testing, and small-batch production, sheet-based processing with the Slot-Die Coater for sheets offers maximum flexibility and control. By selecting the appropriate coating method, researchers and manufacturers can optimize their processes to achieve high-quality, reproducible pharmaceutical and medical coatings.
If you're looking for a precise and reliable slot-die coating solution for your pharmaceutical or medical application, contact us today to discuss how our Laboratory Roll-to-Roll Coater and Slot-Die Coater for sheets can support your research and production needs.